Plan Cost Centers
Quantity, activity, and task-related annual planning as described in previous posts generate the orders for the cost center managers responsible for implementation. Like every manager, they are responsible in their area for QQDR: qualities, quantities, dates, and results (see the post “The management cycle determines the value types”). The performance requirements arise from:
-
- the planned production quantities envisaged,
- the necessary internal services provided, and
- the planned internal tasks.
As a first step, cost center managers must therefore consider what services or results their area must deliver. From this, it can then be derived which staffing levels and which assets are required for this. The requirements are derived from the plans already drawn up:
-
- From the planned production quantities, the planned activity levels of a production cost center can be derived with the help of the work plans. From this, the personnel requirements for the production-related work are determined.
- From the internal tasks planned for the given cost center, the hourly requirements for work that is not directly production-related are derived. These are the working times for cost center management, training and education, inspection work, participation in projects, and attendance at meetings of all types.
- The machines and installations installed in a cost center largely determine how much activity will have to be obtained from internal service providers (workshops, maintenance, internal transportation, energy, and so on).
The head of the Stamping cost center has the following planning basis concerning activities, employees, and machinery:
-
- According to production planning, his cost center should be ready for an activity level of 338,855 personnel minutes (Pmin).
- For the stamping work and for internal tasks, 4 full-time positions are required (including the manager), as each employee is planned with a net annual presence time (vacation public holidays and other absences already deducted) of 102,000 minutes (4 x 102,000 = 408,000 minutes).
- The capacity of the installed machines is still sufficient at 435,840 minutes.
On this basis, he begins to plan the primary costs to be incurred for the planned activity. To do this, he receives a list of the plannable cost types from the controller. This is shorter than the list of the expense types in accounting as it is defined to plan the costs of this cost centers consumption:
-
- To do this, the personnel costs including all social welfare costs are prepared in the personnel area and reported to the cost center manager as a total amount. Since the cost center manager cannot change the rates for additional wage-dependent costs (for example, insurance, vacation), one aggregate cost category for Personnel costs is sufficient. This makes planning and control easier.
- The controller prepares the imputed depreciation amounts in Fixed Asset Accounting based on the assets installed in each cost center and reports this information to the cost center manager.
- Primary costs are characterized by the fact that they come from outside the company and, with few exceptions, are always posted in Accounts Payable or Payroll Accounting. If such costs are to be provided in the cost center (office materials, supplies, etc.), the planner consults invoices from previous years, maintenance plans and other documents to determine the planned cost amount.
This procedure is directly linked to the process of management by objectives. Once the cost center manager has prepared his cost and activity planning, he agrees on the target cost center budget with his boss. For this reason, the cost center plan may only contain amounts and cost elements that the responsible person can influence directly.
Cost center planning does not yet contain the planned costs for internal services provided. These are called secondary costs as they stem from another cost center. In the table of planned internal activities in the post “internal services provided” it was shown that in the plan year 240 service-hours are to be obtained from the maintenance and repairs cost center (330). Its hourly rate is 38.95, which results in a debit of 9,348. The planned cost for energy consumption was calculated accordingly. A total of 536 is planned for this. The complete planned costs of the stamping shop are as follows:
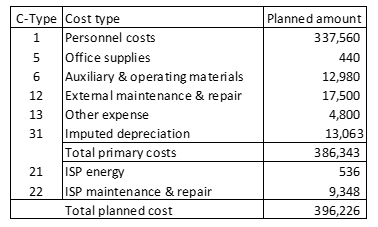
The detailed sequence of the calculations can be traced in the simulation model accompanying Management Control with Integrated Planning – Models and Implementation for Sustainable Coordination.
To use the cost center plans in product calculation the next post will first provide clarity about cost terms in the management control system.